Opening Ceremony of the 33rd EICF International Conference & Exhibition, including EICF Welcome, UK Foundry Sector Review and Key Note presentation on Conference Theme
EICF Chairman , Dr Julio Aguilar shall be greeting attendees to the 33rd EICF International Conference & Exhibition
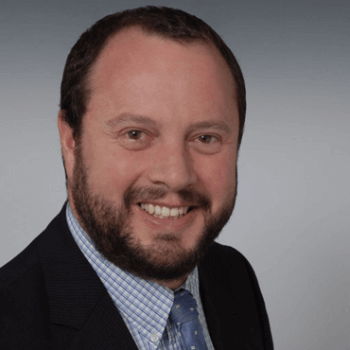
Cast Metals Federation is the UK National Foundry Association, representing Members’ interests at local, regional, national and international levels, promoting the UK foundry and casting industry,
CMF Chairman, shall be presenting a portrait of the Foundry Industry in the United Kingdom , providing some insights of the relevance and economical impact of the sector
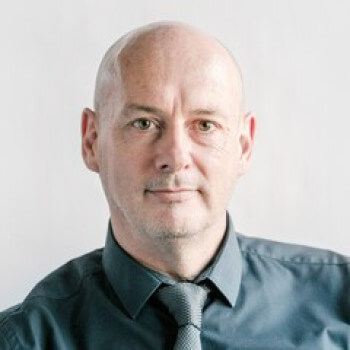
This two part presentation will discuss the importance of ensuring the supply chain for foundry alloys and consumables can impact product quality and cost; and the criticality of putting health and safety at the centre of foundry process improvements.
Challenges for the Supply Chain will focus on the issues that foundries face in delivering components at the correct cost, lead time and quality by addressing the materials that we use, the processes (and equipment) we operate as well as the digital journey. Investment casting for aerospace is a highly regulated field. The media attention to aerospace safety is guaranteed, if product safety is brought into question then reputational damage is assured. The investment casting of Ni Superalloys involve many processes and materials, for example, a typical shell material contains six different material components, and they are supplied by five separate companies. The complexity of managing materials and casting processes will be discussed in the presentation.
Enhancing HSE in the Foundry Environment will answer the question why is good HSE practice good for business? Foundries are complex factories with several processes operating. Melting metal is fundamental to the foundry process, but there are many other manufacturing operations that are associated with casting. The presentation will look through the various challenges of health and safety in the foundry from mould making through to the inspection operations prior to delivery, and give examples of where good HSE practice can save money for the foundry.
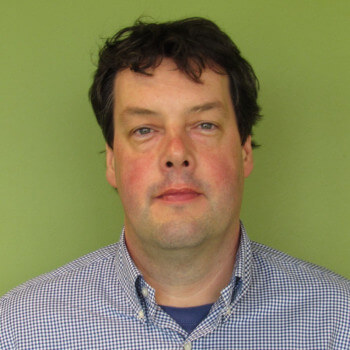
Brief description of the Conference & Exhibition, structure, events and schedule
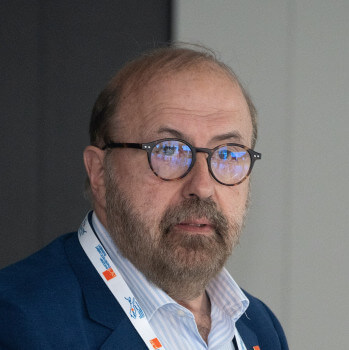
Coffee Break & Exhibition time
Technical Conferences & Cases Studies on Track 1 & Track 2 (see associated tabs for details)
Lunch shall be available during the Exhibition
Technical Conferences & Cases Studies on Track 1 & Track 2 (see associated tabs for details)
Coffee Break & Exhibition time
Technical Conferences & Cases Studies on Track 1 & Track 2 (see associated tabs for details)
Day one of the 33rd EICF Conference & Exhibition ends
=====================================================================================================================
Keynote Presentation in Association with the first seminar on Additive Manufacturing and Investment Casting "AMIC"
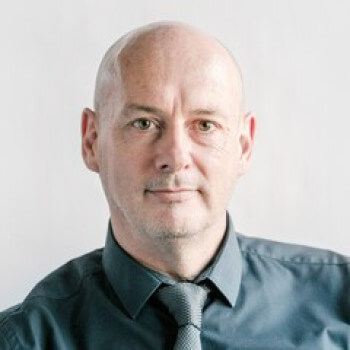
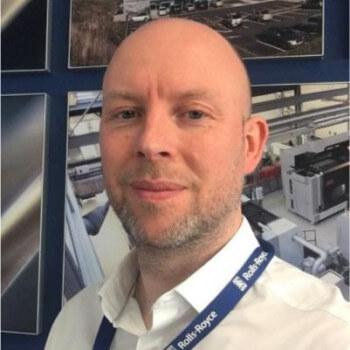
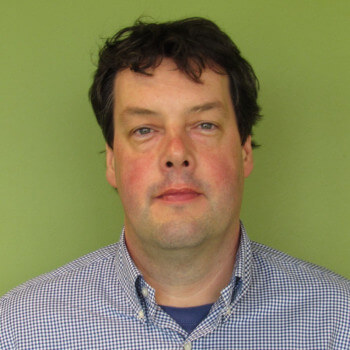
Coffee Break & Exhibition time
Technical Conferences & AMIC Seminar on Track 1 & Track 2 (see associated tabs for details)
Lunch shall be available during the Exhibition
Technical Conferences & AMIC Seminar on Track 1 & Track 2 (see associated tabs for details)
Coffee Break & Exhibition time
Technical Conferences & AMIC Seminar on Track 1 & Track 2 (see associated tabs for details)
Day one of the 33rd EICF Conference & Exhibition ends
Presentations on technology equipment supporting an improved Health & Safety use
Throughout the furnace industry, health and safety issues can arise from a lack of risk control and prevention, a lack of maintenance, improper use of equipment and a lack of suitable training, all of which are fully preventable.
In the field of vacuum melting and heating technologies, there are a number of specific safety considerations, including operational temperatures exceeding 2500°C, processing materials under vacuum or other potentially hazardous atmospheres, together with other conventional risks, such as electrical risk, EMF risk, risk of entrapment, confined spaces, asphyxiation, working at height, etc.
Consarc are committed to ensuring that health and safety is forefront of the furnace design process and in the use of the vacuum equipment, throughout its entire life cycle. This article describes the main features of modern vacuum equipment designs, specifically developed towards the target of safe furnace processing with extended machine life.
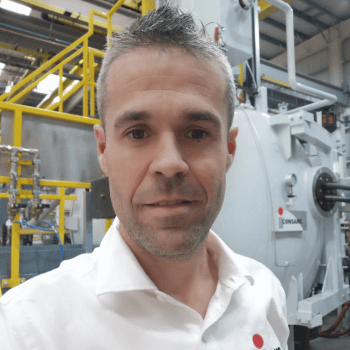
Automation / Robotic equipment is the need of time for automating investment casting foundries. It can enhance safety drastically in the foundry. The most apparent safety concern in foundry is burning due to working with extremely hot molten metals. Handling high temperature material along with heavy weight material is always a cause of concern in terms of safety. Robots and automation system can tackle these challenges very easily and can make the process very safe. These eliminate the risk of burns and other injuries associated with foundry work. Foundry safety programs should also focus on other health and safety concerns i.e. dust inhalation, heat stress, and vision protection. While automation offers many advantages in the investment casting process, there are several challenges that need to be addressed for effective implementation. Automation in investment casting faces challenges related to cost, complexity, technical & operational skills, quality control and most importantly cultural and workforce resistance. While the potential benefits are significant, overcoming these hurdles requires careful planning, investment and training. Flexibility, worker training, and integration with legacy systems are key factors to consider for a successful transition to automation. Few challenges can be overcome by some other advance technical solutions such as Radar technology, Physical ladle tracking (PLT), RFID, IOT, AI automation and cloud based control system along with high-tech protective gear and advance ventilation system. Adhering to strict Safety protocols, SOP can be made possible through technology and Adopting lean manufacturing principles.
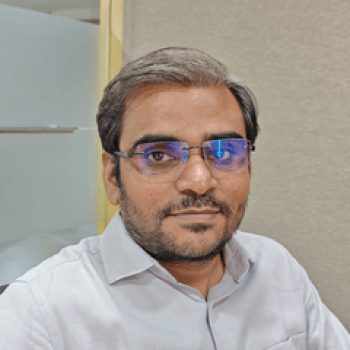
Lunch shall be available during the Exhibition
Presentations on process inovation related with the development of materials of enhanced properties and more efficient processes to be used in the Investment casting Manufacturing Technology
Tecnalia, in collaboration with EIPC, is developing high-performance aluminum castings by investigating Al-Cu and novel aluminum multicomponent alloys. The project employs Integrated Computational Materials Engineering (ICME) methodology, developed by TECNALIA, for alloy design. This approach is coupled with detailed analysis of the investment casting process under various cooling conditions. The optimization of heat treatment processes for these new alloys is also a key objective of this research. The research encompasses a comprehensive study and validation campaign, including pilot-scale castings performed in TECNALIA's CIRMETAL facility, along with microstructural and mechanical testing of samples. This innovative approach aims to enhance the properties of aluminum castings for aerospace applications, potentially opening new market opportunities for high-value components. This presentation outlines recent progress in alloy design, casting trials, and preliminary property assessments. It also delineates upcoming tasks, including further optimization of solidification control methods and extensive material characterization, to achieve the project's objectives of producing superior aerospace components.
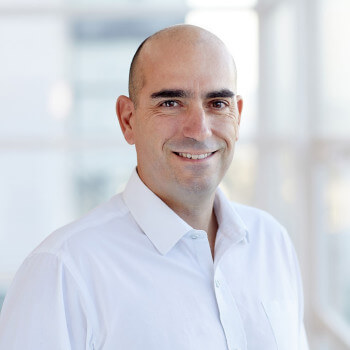
Ceramic filters have been an essential component of the investment casting runner system for decades, delivering significant yield benefits by reducing inclusion and secondary grain scrap. Because of their performance enhancement, filters have been the subject of much academic and industrial interest, with experimental quantification of filter efficiency typically taking the form of water-based experimental rigs, or mechanical testing of test pieces cast with different filter and runner configurations. In foundries, costly large-volume trials are required to examine the relative performance of filters in terms of yield results.
This body of work sought to develop methods to quantify filtration efficiency on an established production casting process in an experimentally efficient manner and without compromising the saleability of cast components. This was achieved by casting moulds, sectioning filters, and annotating filtrate location, size, and type on reflective microscopy images. SEM-EDX was also used to determine composition of a subset of the filtrate. Next, the rate of decay of concentration through the depth of the filter was modelled by curve fitting to previously derived analytical expressions for deep-bed filtration. Modification of this expression to consider inclusion concentration as an empirical cumulative distribution function delivered large improvements in the confidence of the fitted model, thereby requiring fewer cast cycles to compare filter performance.
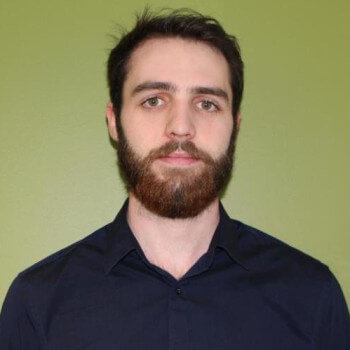
Coffee Break & Exhibition time
Presentations on IC Market Status: Covering economic regions such as Europe, North America, China, Japan, and Rest of Asia, concluding with a comprehensive global perspective.
European Market Review as per Market segments
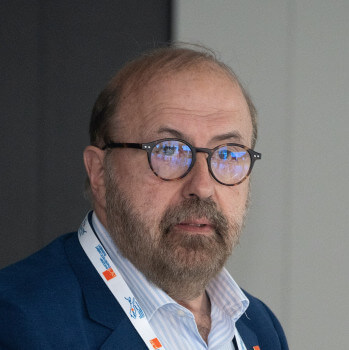
North America Market Review as per Market segments
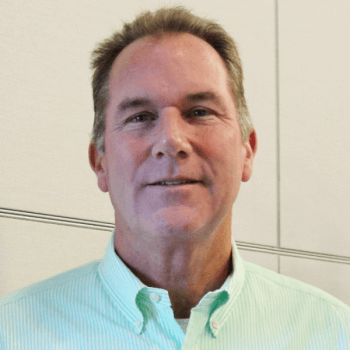
China Market Review as per Market segments
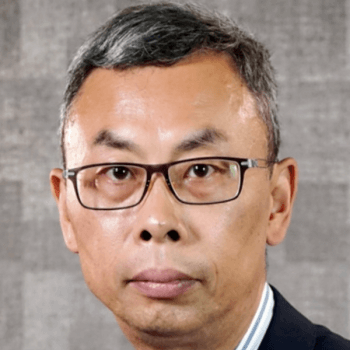
Japan Market Review as per Market segments
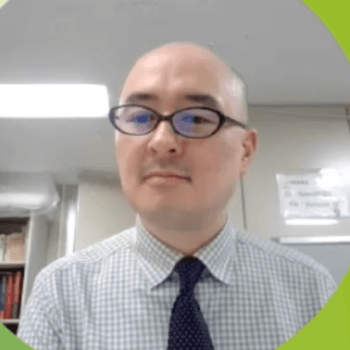
A global perspective Market Review as per Market segments
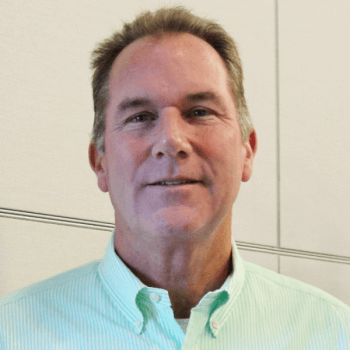
Day one of the 33rd EICF Conference & Exhibition ends
=====================================================================================================================
Presentations on Smart Technological Processes Supporting the Recycling of Key Materials in Investment Casting Manufacturing Technology
Wax reclamation has been around since 1970 when Ben Verta Sr. first started dewatering and filtering investment casting wax for Howmet Circast for use as sprue wax. The need for such low cost material has been sustained for commercial casters and aerospace casters alike. However it is not cost that drives this market. Petroleum, or the limited availability of such petroleum waxes and feedstocks from the ink driven resin market cause shortages. Wars and their interference with supply routes or manufacturing originating in war zones is a common concern in the EU currently. Never the less, foundries need to secure supply chains to guarantee their production capabilities. Renew resolves 90% of these issues.
What is RENEW? It is a chemical process where a dewax containing contaminants and broken carbon chains can be rebuilt back to the original specifications and quality. This is technology beyond normal reclamation or reconstitution practices used in the art of wax making.
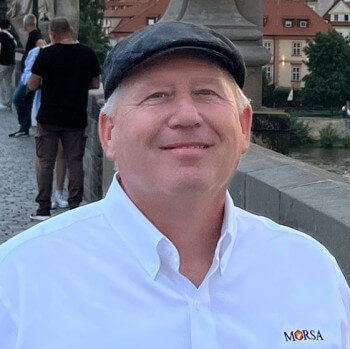
In the summer of 2024, the VIM B52 scrap remelter was successfully commissioned at Danieli’s research center in Buttrio, Italy, ahead of its delivery to the end customer for integration into their production process. This state-of-the-art furnace is specifically designed to meet the needs of investment casting facilities, enabling efficient in-house recycling of superalloy revert materials into barstock. The in-house recycling capability significantly reduces the carbon footprint and enhances supply chain efficiency by cutting transportation costs and minimising capital tied up in rolling stock. Leveraging several innovative technologies, the VIM B52 eliminates the need for extensive scrap preparation, such as cutting or breaking. This paper outlines the key technological advancements of the furnace, details the results achieved during commissioning, and examines its seamless integration into the customer’s production workflow. Furthermore, the paper highlights the resulting supply chain improvements, carbon footprint reductions, and the broader sustainability benefits derived from this groundbreaking innovation.
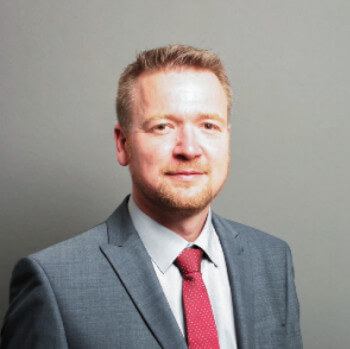
Lunch shall be available during the Exhibition
Presentations on advanced process control and innovation materials related with the Shell Systems
The temperature of a foundry’s slurry is often measured but little understood. Temperature is regularly monitored as part of standard slurry testing; however little time is given to understand how it can affect the performance of a slurry or shell system.
This paper aims to assess the underlying fundamental questions raised in temperature measurement of a slurry: Where is the heat generated? How does it affect slurry control? Does it affect a shell’s performance? This paper presents fundamental work carried out to answer these questions, enabling process engineers to understand the sensitivities and act accordingly.
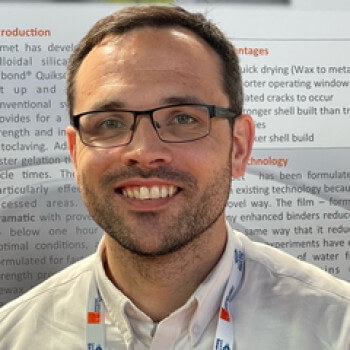
The complexity of casting designs is ever-evolving and are creating unique challenges for suppliers to help foundries address. The cost-conscious nature of investment casting and rising inflationary headwinds drive urgency to innovate more versatile shell systems that offer engineered performance with commodity refractory flours. The engineered performance to be presented include increased throughput by reducing cycle time, shell build uniformity, binder compatibility with fused silica, aluminosilicate and alumina refractories.
A background of the technology design and application testing will be presented herein.
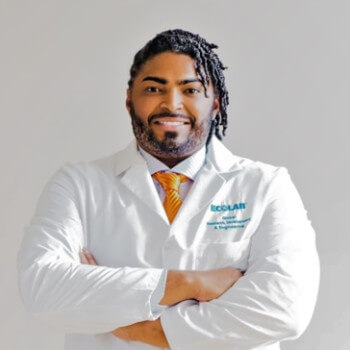
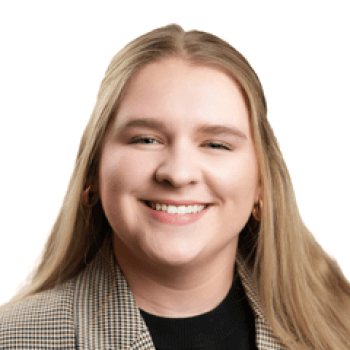
Coffee Break & Exhibition time
Presentations shall focus on strategies, technologies, and best practices for reducing defects in investment casting, highlighting their impact on sustainability
Microporosity in investment castings is difficult to avoid and limits the mechanical properties and fatigue behaviour of critical parts such as tur-bine blades. Its presence can lead to increased scrap rates, reduced com-ponent lifespans, and greater inspection requirements during operation. Therefore, a reduction in microporosity can have a significant impact on the environmental performance, safety and durability of investment cast-ings. Traditional methods to optimize the casting process through experi-mental trials are both time-consuming and expensive. As a result, numeri-cal simulations are increasingly used to accelerate the development pro-cess. However, the prolonged simulation times – often spanning several hours – severely limit their utility in optimization loops. To address these limitations, artificial intelligence (AI) offers a promising alternative through the introduction of machine learning (ML) models that can rapid-ly estimate the effects of changes in geometric and process parameters on microporosity. However, due to the high cost and time demand of casting trials, sufficient experimental data is rarely available to train ML models with the necessary predictive accuracy. In this contribution, we show that simulation-generated data can be used to effectively overcome this bottle neck by providing the datasets needed to train ML-models. In the optimi-zation of a complex setup involving 18 test specimens, numerous simula-tions of critical component regions were used to generate training data. The resulting ML model was subsequently employed to guide engineers in designing gating systems and selecting process parameters that mini-mize microporosity. The integration of this ML-driven approach into the casting design process significantly reduces the development time.
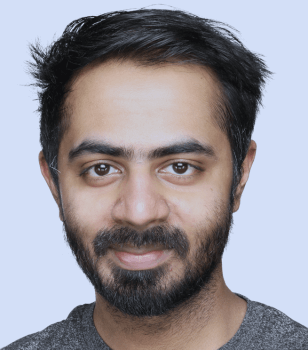
Today, foundries have to develop strategic solutions to meet changing market requirements. This affects the entire value chain. Decisions need to be made that have a significant impact on cost effectiveness and sustainability. For traditional investment casting in particular, innovative processes, materials and methods are an opportunity to sustainably improve the entire value chain. In the age of digitalization and machine learning, such new developments can and must be accompanied by a digital twin.
This paper shows selected examples of how a digital twin is being used also in other industries and how investment casting can learn from them. One example from the automotive industry deals with the production of large die-cast components (so-called Mega-Casting). Here too, costs and the CO2 footprint are of great importance. What does Mega-Casting and investment casting have in common? Both have to produce functional, structurally sound cast components and products, at a price that is acceptable to the market conditions. This casting has to have the right mechanical properties, otherwise it won’t pass the crash tests and be the right shape. How does the automotive industry develop this type of casting? The short answer is ‘as quickly and cheaply as possible’, which involves using the use of simulation tools. The paper will show how the whole casting, fettling, heat treatment and machining process chain can be simulated, with an emphasis on shape change, distortion, and contraction.
In a second example of an investment casting, the manufacturing costs are directly taken into account when assessing the process. Here, the quality requirements and costs are in competition. Virtual experimentation is used to show how all requirements are evaluated in order to find an industrial solution which achieves the right balance between quality, costs and sustainability.
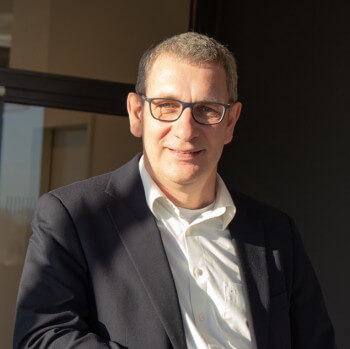
Porosity naturally occurs during the solidification process in investment casting. As the material solidifies from the outside, pores form in the centre of the casting. These pores reduce mechanical properties, compromising the reliability and performance of the final product and limiting its suitability for high-performance applications. This paper examines the work that has been done on applications of hot isostatic pressing (HIP) to densify investment cast components. The performance of investment cast components before and after HIP-treatment will be examined, highlighting the clear advantages of HIP over conventional heat treatments in improving mechanical properties. Notable improvements include stress-rupture life and creep resistance after undergoing HIP-treatment. Further advancements were observed when applying novel HIP-treatment techniques, such as HPHT® and URQ®, to investment cast components—signaling the crucial role of HIP for the investment casting industry.
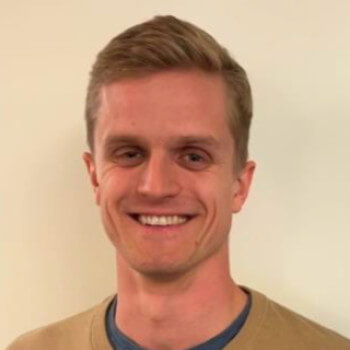
Day one of the 33rd EICF Conference & Exhibition ends
Presentations on advance and innovation on automation technologies linked to IC manufacturing processese
Precise monitoring and control of slurry viscosity and weight are essential for producing high-quality shells. Torsional resonator-based sensors offer continuous, in-situ measurement of slurry viscosity and density, eliminating the need for laboratory sampling. However, these sensors are susceptible to deposit buildup, which can compromise measurement accuracy. For some slurry compositions, maintaining a deposit-free surface requires frequent cleaning. While this maintains sensor cleanliness for many shell rooms, manual cleaning schedules present a challenge for automation and creates additional workload for operators.
This work introduces a novel solution to maintain sensor cleanliness and ensure accurate, drift-free measurements of slurry weight and viscosity. By applying low-frequency, high-amplitude vibrations, the sensor effectively repels deposits. A Rheonics SRD sensor has demonstrated sustained, deposit-free operation for over two months in challenging, deposit-prone slurry tanks, eliminating the need for manual cleaning. Users have validated the SRD sensor's accuracy by comparing its viscosity, density, and temperature readings to those obtained from Zahn cup measurements, observing consistent trends.
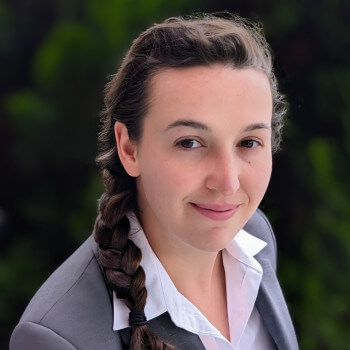
The role of automation in expanding the application of SX casting process modelling in Rolls-Royce is proving transformative. Current modelling processes are hindered by reliance on skilled resources requiring both comprehensive casting process knowledge and NX CAD capabilities. These resources face prolonged lead times for geometry and mesh creation, simulation preparation, and subsequent analysis, while risking inconsistent reporting and model generation. This issue is further exacerbated by limited modeller capacity and high demand that can limit innovation opportunities. Automation tackles these challenges by enabling the generation of multiple geometric and process variations, alongside automatic model launch, analysis, and technical reporting with high consistency standards. It evolves as new methods and improvements emerge, becoming an integral part of the process. These developments significantly expand modeller capacity, enabling process innovation, slashing lead times—saving weeks of effort and converting processing times to mere minutes—while maintaining full control over key intellectual property.
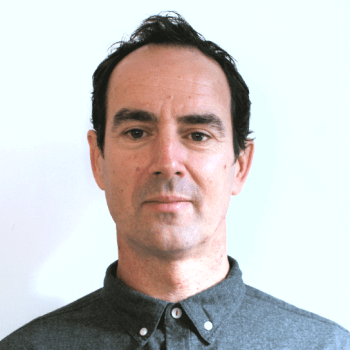
Lunch shall be available during the Exhibition
Presentations on Smart Technological Processes Supporting the Recycling of Key Materials in Investment Casting Manufacturing Technology
The increasing global demand for superalloys, coupled with declining virgin material reserves, highlights the urgent need to rethink how we manage, and value revert materials. Far from being "scrap," revert is a high-tech raw material that drives cost savings, reduces environmental impact, and enhances resource resilience—all while maintaining the same quality as prime materials. By integrating revert into circular supply chains, the industry can reduce dependency on primary raw materials and foster sustainable growth. Revert materials offer significant benefits, including cost reductions for melters, lower energy consumption, and decreased reliance on mining and refining virgin resources. Proper handling, segregation, and testing by accredited companies are essential to ensure precise chemistries, enabling casting facilities to achieve exact specifications. This practice not only supports operational efficiency but also aligns with global sustainability goals by minimising waste and maximising resource use. This presentation will examine the evolving industry standards supporting the adoption of revert materials, the role of innovative management practices in maximising recovery, and the critical importance of a shift in perception. By redefining revert as a high-tech raw material, rather than "scrap," the industry can unlock its full potential and contribute to a more sustainable and resilient supply chain. Attendees will gain insights into how these practices are reshaping the future of superalloy casting while promoting sustainability and operational excellence in a resource-constrained world.
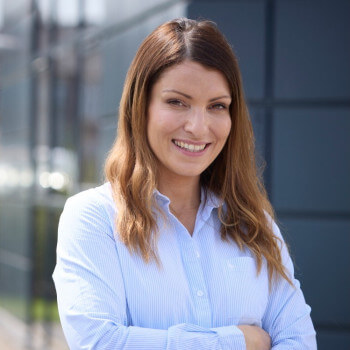
Dewaxing in the autoclave is a crucial step in precision casting, responsible for nearly 90% of cracks in ceramic shells, primarily located on their inner surface. Rigorous control of this process is essential to ensure clean and defect-free shells, thus minimizing the risk of structural weaknesses and optimizing the accuracy of the final parts. The presentation will address the key role of the autoclave in this process, detailing parameters such as temperature, pressure, and cycle duration. The thermal expansion difference between the wax and the shell requires good permeability of the shell to allow the evacuation of molten wax without damaging the mold. It will be discussed, with literary references, how steam plays an essential role in doubling the thermal conductivity of the shell. A brief comparison between the autoclave and the flash oven will also be made. Additionally, we will highlight the importance of non-destructive testing (NDT) and compliance with essential Pressure Vessels Directive about safety and endurance of the autoclave body. The presentation will also include the optimal water properties required to ensure consistent, durable, and reliable performance. Finally, a customer case study will illustrate the tangible benefits and results achieved through the use of our last generation autoclaves for efficiency and safety.
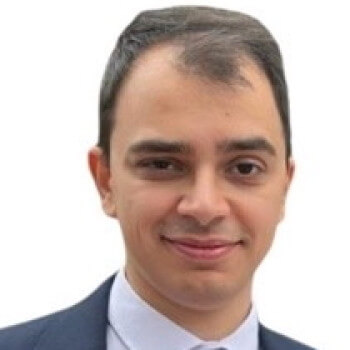
Coffee Break & Exhibition time
Presentations will explore investment casting supply chain trends, challenges, and opportunities across, materials, strategies and technologies
The new marketplace disrupted by COVID, post-COVID, and emerging global geopolitical conflicts required different supply chain approaches to ensure stable production. During COVID, we realized that the supply chain was a vulnerable element. After the lockdowns, related manufacturing shutdowns, and supply chain bottlenecks came the post-COVID economy. In the aftermath of the pandemic, we were faced with a still partially disrupted global economy. This was characterized by the need to ramp up production while replenishing inventories. In some cases, overstocking led to strong demand for products, followed by a period of lower order volumes. Then came a situation of increasing geopolitical tension and conflict, which also had a short-term and lasting impact on the supply chain. And now sustainability is emerging as the next big headline that will have a significant impact on supply chain strategies. As a result, there is a strong need for solutions to respond to these situations. This paper presents a variety of logistics approaches to meet customer needs in these new market situations. It presents case studies of various supply chain solutions that have been proven in practice. These include flexible supply concepts as well as long-term solutions.
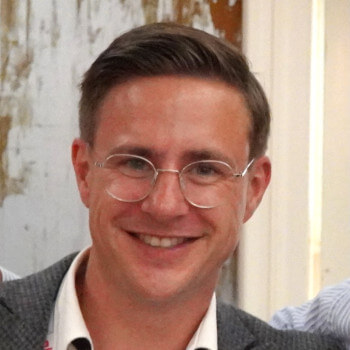
Most components of an investment casting wax are petrochemicals and as such related to this industry. Besides changes in geographical supply situations, there are challenges in logistics and megatrends in the petrochemical industry. Due to the lack of Russian gas & oil in combination with further EU legislation on CO2 reduction and general market dynamics, there is a fast reduction in the supply of European petrochemicals. This paper is showing the underlying forces and considerations for these reductions and their impact on the supply chain. Paramelt is responding to these trends as to keep the high level of diversification, increasing stocks of raw materials, local production sites and close contact with its main global suppliers. Another route to increase the chain resilience and cost stability of a casting wax and to reduce the carbon footprint of a foundry, is to recycle the autoclave wax of investment casting foundries. This paper shows the current capabilities to produce (partly) runner and pattern waxes coming from these autoclave waxes and the batch to batch variation achieved. As latest innovation to reduce the carbon footprint and increase the safety of a foundry, new pattern waxes are discussed with very low injection temperatures in the range of 45-48°C. Besides safety and costs, the lower injection temperatures will help as well to eliminate problems with e.g. cavitation and cracks in the wax patterns and increase the overall productivity of an investment casting foundry.
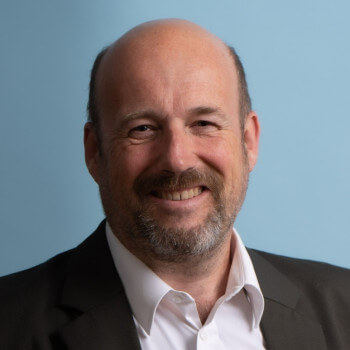
Day one of the 33rd EICF Conference & Exhibition ends
=====================================================================================================================
Exploring Synergies: Presentations on Additive Manufacturing and Investment Casting Integration
Highlights include advancements in AM pattern-making, hybrid manufacturing processes, enhanced design capabilities, and material innovations transforming the investment casting industry.
Investment casting is a tried-and-true method for creating intricate and complex metal parts. But the combination of investment casting and 3D printing using stereolithography is opening up new possibilities and advantages for manufacturers.
In this presentation, you'll gain invaluable insights into the benefits of adopting 3D printed patterns over traditional production methods and learn how to overcome the pitfalls associated with investment casting.
1. The Advantages and Limitations: Understand the unique advantages that result from combining investment casting and 3D printing.
2. Ideal Applications for 3D Printed Patterns: Discover the industries and applications where 3D printed patterns truly shine.
3. Designing with Stereolithography: Learn the intricacies of designing 3D printed patterns using stereolithography.
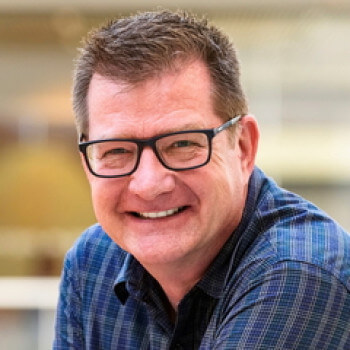
In an era of increasingly complex casting designs and a growing shortage of skilled labor, producing high-quality investment casting components has become a significant challenge. However, leveraging proven 3D printing technologies like PMMA in conjunction with investment casting offers a powerful solution to help foundries overcome these pressures. By integrating additive manufacturing (AM) with traditional metal casting, foundries gain unparalleled design freedom, enabling the creation of optimized, intricate geometries that were once difficult or impossible to achieve through conventional methods.
This hybrid approach not only enhances the ability to manufacture complex designs but also provides long-term benefits, including reduced lead times, improved quality, and greater flexibility in both prototyping and serial production. As the influence of metal additive manufacturing (Metal AM) grows, PMMA-based 3D printing technology allows investment casting companies to maintain their competitive edge by offering an efficient, cost-effective method to produce high-precision components that can evolve alongside rapidly advancing design demands.
In this presentation, we will explore how foundries can seamlessly integrate AM technology into their existing casting processes, highlighting the technical advantages and long-term business benefits. From improving quality and increasing capability to remaining competitive in an evolving market, this approach empowers manufacturers to meet today’s engineering challenges while preparing for future success.
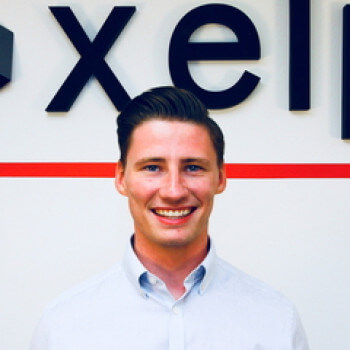
Lunch shall be available during the Exhibition
Exploring Synergies: Presentations on Additive Manufacturing and Investment Casting Integration
Highlights include advancements in AM pattern-making, hybrid manufacturing processes, enhanced design capabilities, and material innovations transforming the investment casting industry.
In recent years, 3D-printed ceramic molds and cores for investment casting have shown great potential for producing geometrically complex components, particularly for low-volume productions. Ensuring surface quality is critical in this manufacturing process. This study employs machine learning (ML) to predict surface roughness of 3D-printed ceramics by investigating three key variables: angle, printing direction and measurement orientation. Using a sloped geometry (angles 5° to 85°, in 5° increments relative to the Z-axis), surface roughness measurements were conducted across normal and overhang printing directions, in two orientations (parallel and perpendicular to stacking layers). Multiple machine learning models, including Support Vector Machines (SVM), CatBoost, Random Forest, and Long Short-Term Memory (LSTM) networks, were then developed and compared. Additional test samples with non-standard angles (such as 51.7°) were printed and measured for validation. The models were further evaluated based on their ability to predict surface roughness across these samples. Results demonstrated that the LSTM model had the best performance giving the lowest root mean square error (RMSE), which highlights the model’s potential application to optimize printing conditions and improve manufacturing precision, advancing the use of 3D-printed ceramics in investment casting.
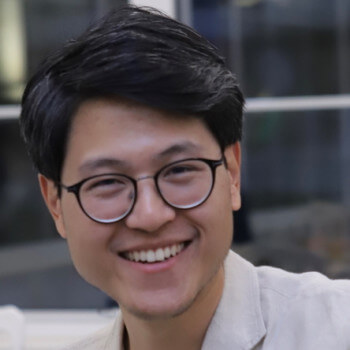
The integration of artificial intelligence (AI) and full-process automatization in additive manufacturing (AM) represents a transformative paradigm to reach the new era of manufacturing. By addressing key challenges such as design complexity, printing parameters optimization, and production scalability, AI-driven solutions enable real-time decision-making and predictive analytics across the entire AM workflow. Automatization enhances production efficiency through seamless coordination of pre-production, in-situ monitoring, and post-processing, reducing waste and improving product quality. Together, these advancements position AM as a pivotal solution for manufacturers, offering unprecedented flexibility, cost-effectiveness, and sustainability. The adoption of AI and automation in AM not only accelerates innovation but also bridges the gap between traditional manufacturing and the digital era, making it an indispensable tool for the future of production systems.
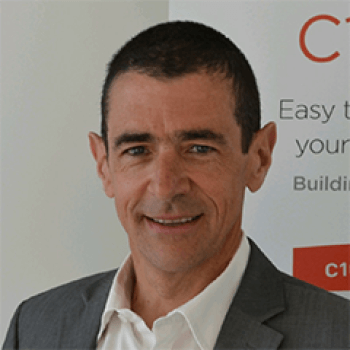
Coffee Break & Exhibition time
Exploring Synergies: Presentations on Additive Manufacturing and Investment Casting Integration
Highlights include advancements in AM pattern-making, hybrid manufacturing processes, enhanced design capabilities, and material innovations transforming the investment casting industry.
The Investment casting (IC) industry is increasingly adopting additive manufacturing (AM) techniques to achieve new levels of precision and design complexity. However, integrating AM into IC workflows for demanding applications, such as single-crystal casting, introduces significant global process challenges. This study focuses on the development of a silica-loaded photocurable slurry optimized for top-down Digital Light Processing (DLP) printing, addressing critical gaps in material performance and process compatibility. The aim is to develop a material that overcomes the limitations of IC-compatible slurries while ensuring scalability and productivity. Existing research has explored AM slurries, but few have tackled the dual challenge of optimization for both AM processes and IC performance. This work tries to bridge that gap through innovations in material chemistry, and process optimization. The study will strive to demonstrate that not only the slurry allows to print acceptable parts, but as well to make them compliant for us in IC processes.
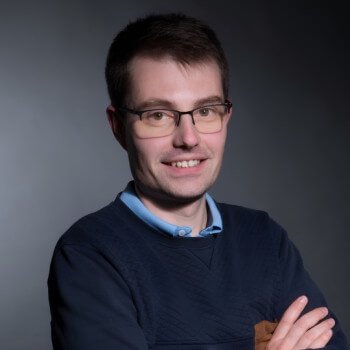
3D printing has been demonstrating its value to create casting patterns for more than 25 years. At that time, 3D Systems introduced QuickCast® — enabling companies to produce high-precision, lightweight patterns directly from CAD without tooling, allowing engineers to design higher-performance parts with full design flexibility and no sunk costs in tooling. Today, 3D Systems is pioneering the next frontier in investment casting.
The company’s PSLA (projector-based SLA) technology is a groundbreaking platform enabling the rapid production of high-quality investment casting patterns. During this presentation, Patrick Dunne, 3D Systems’ VP, Application Innovation Group & Technical Fellow, will delve into how this technology can help foundries achieve unprecedented speed and precision.
By delivering production-grade patterns in a single automated process, 3D Systems’ PSLA accelerates workflows, minimizes material waste, and ensures precision at every stage. This transformative platform combines speed, versatility, and reliability, empowering foundries to meet evolving industry demands.
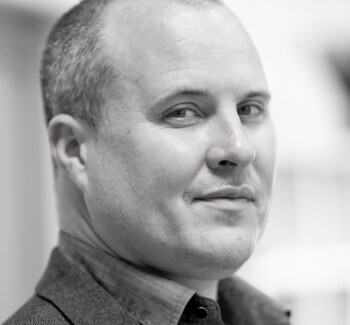
In recent years, ceramic materials have gained significant attention in additive manufacturing, particularly for their application in producing molds for investment casting. This technology offers an efficient and flexible solution for fabricating geometrically complex components, even at low production volumes, surpassing the capabilities of traditional manufacturing methods. In this study, ceramic shells for investment casting were fabricated using commercially available ceramic-filled resins enhanced with cobalt aluminate (CoAl) particles via the lithography-based ceramic manufacturing process. These shells were evaluated in an Inconel 718 investment casting process to assess their performance.
The results demonstrate the feasibility of 3D-printed ceramic molds, confirming their ability to suppress the growth of undesirable coarse-grained structures while promoting the formation of fine-grained microstructures. This effect, previously observed in traditional casting processes using CoAl additives, was found to be equally effective with 3D-printed molds. The refinement of grain structure significantly improves the physical and mechanical properties of nickel alloy castings, making this approach particularly beneficial for high-performance applications in aerospace and power generation.
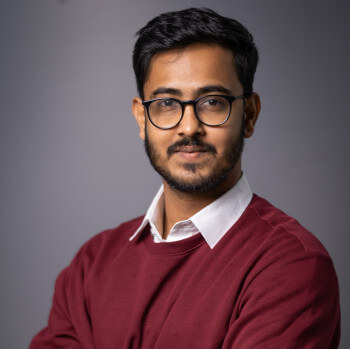
Day one of the 33rd EICF Conference & Exhibition ends
This opening event will provide a relaxed and informal setting for delegates to connect, meet new industry peers, and rekindle existing relationships. Taking place on the first evening of the conference, it sets the tone for collaboration and dialogue throughout the event, allowing a first glance of the Exhibition
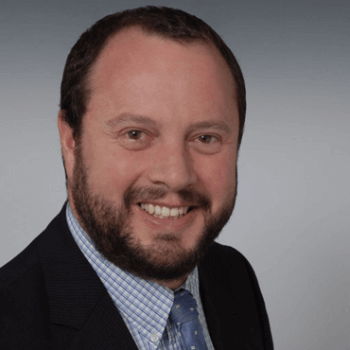
A highlight of the conference, the Gala Dinner will offer a more formal and elegant environment, combining fine dining with opportunities to engage in meaningful conversations. This evening will celebrate the investment casting community, providing a unique platform for networking while enjoying a memorable social experience.